Photovoltaic Backplane Cracking in Material Failure Analysis
Photovoltaic Backplane Cracking in Material Failure Analysis
I. Introduction
When it comes to photovoltaic products, I believe it has become a household name. There are photovoltaic products in ground photovoltaic power stations, BIPV for building integration, solar power highways, energy-saving vehicles, etc. It is believed that the application of photovoltaics will be more extensive in the near future.
Photovoltaic modules are the core components of solar power generation systems, and their service life has a certain relationship with the lamination process, but it also depends on the performance of the raw materials used, the most critical of which is the photovoltaic backsheet. As the outermost layer of the module, the photovoltaic backsheet is in direct contact with the external environment and can withstand outdoor wind, rain, exposure, corrosion and pollution; it is also in contact with the internal packaging material to prevent leakage from the outside and block water vapor from the inside .
Photovoltaic backsheets are composed of polymer materials. Some photovoltaic backsheets will expose obvious quality problems in advance after being used for a period of time, and even lead to module failure. One of the serious problems exposed by the current photovoltaic backplane is the cracking of the backplane. The research found that the backplane cracking problem is mainly concentrated in the 3A backplane. A photovoltaic power station using a 3A backplane has a large number of microcracks on the surface of the backplane after one year of installation, and the cracking ratio of the backplane has exceeded 40% after four years of operation. Around 2016, several GW-level photovoltaic power plants around the world were affected, including domestic western power plants and overseas power plants, seriously affecting the investment income of power plants.
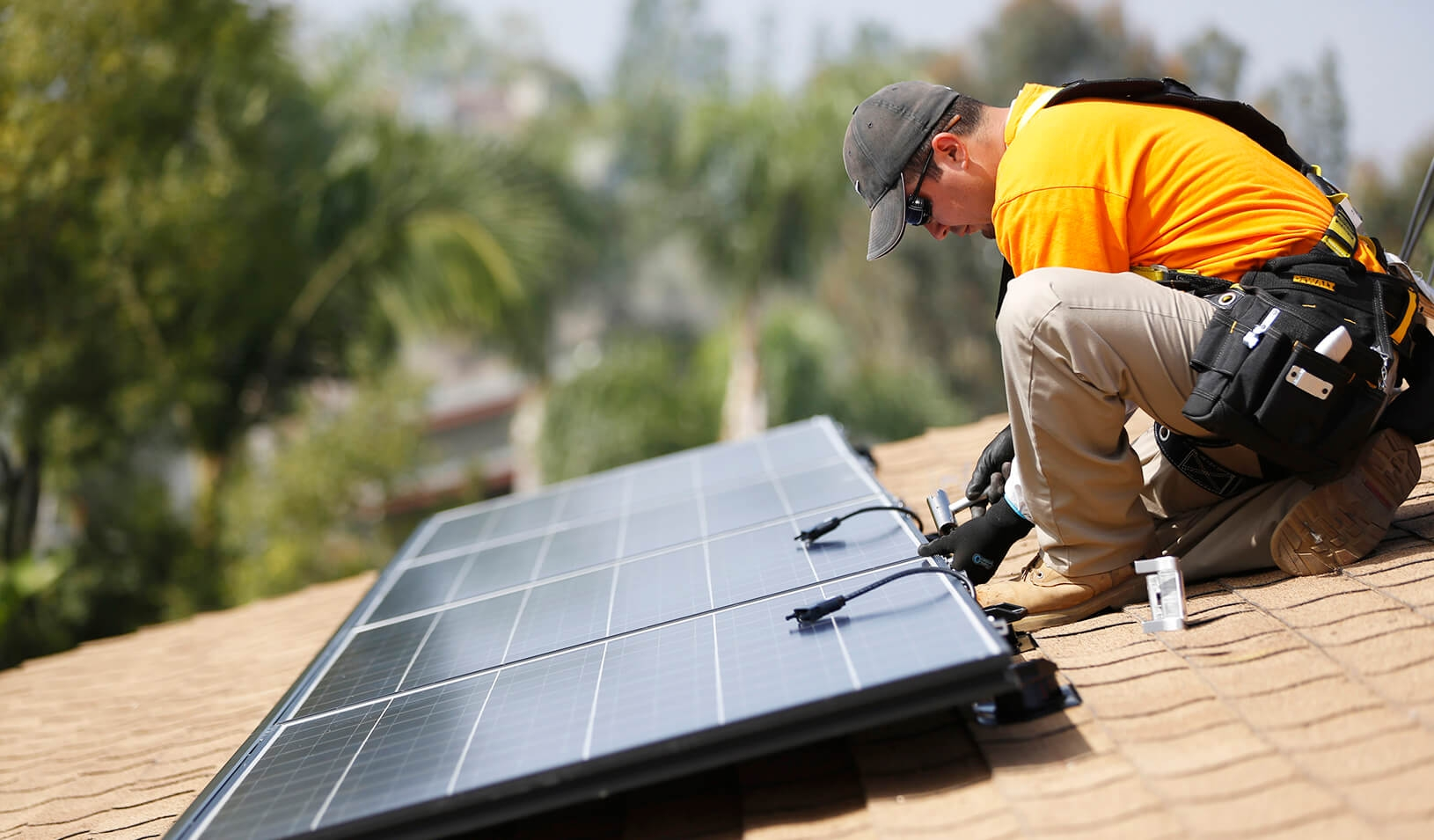
2. Analysis of backplane cracking
In response to the problem of backplane cracking, researchers selected components from around the world that had backplane cracking after 3-6 years of use, and passed a series of chemical and mechanical tests. It turned out that the most vulnerable areas occurred on the inner side of the backsheet, rather than the outer layers exposed to the air. In addition, it was found that most of the cracks occurred between the gaps of the cells.
During the use of photovoltaic modules, the packaging material EVA (ethylene vinyl acetate) will undergo hydrolysis reaction at a certain temperature under the action of water vapor (the photovoltaic backplane has a certain water permeability) and sunlight (including ultraviolet light). Acetic acid is produced, and exposure of the backsheet material to acetic acid causes degradation and cracking. The EVA packaging material on the back of the battery is less hydrolyzed than the EVA in the battery gap due to weaker light. In short, the main reason for the cracking of the backsheet is that EVA is hydrolyzed to produce acetic acid, and the cracks in the gaps between the cells are more due to the fact that the EVA in the gaps is strongly exposed to light.
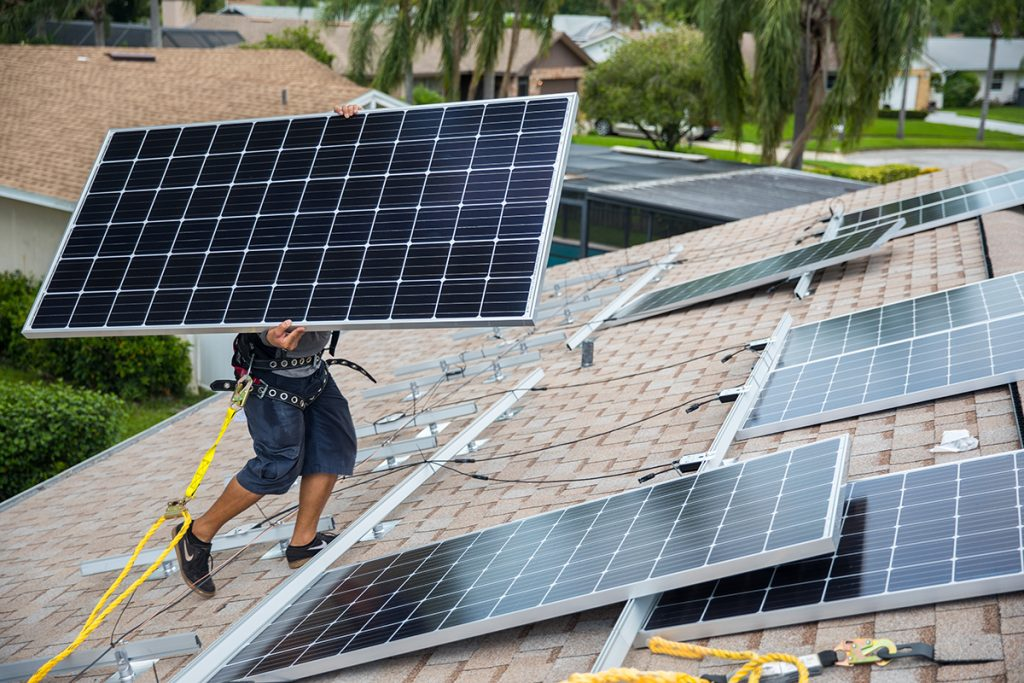
3. Improvement of test conditions
It can be seen from the above analysis results that the conditions required for EVA hydrolysis are: light, water vapor and temperature, all of which are indispensable. Currently, the most commonly used testing standards for photovoltaic products, IEC61215 and IEC61730, only have a separate UV aging series test and a separate high temperature and high humidity DH series test, that is, the conventional UV aging test and high temperature and high humidity DH test cannot be simulated. The effect of EVA hydrolysis reaction on the overall life of components. The UV+DH composite aging environment chamber can effectively verify the ability of component materials (including the back plate) to resist various aging properties in a complex test environment.
The UV+DH composite aging environment chamber is to combine two independent aging tests (UV+DH) to realize the simultaneous operation of two test items (UV+DH), that is, to conduct ultraviolet aging tests in high-temperature and high-humidity environments. It can be widely used in the weather resistance test of photovoltaic connectors, photovoltaic backplanes, and photovoltaic modules (small size).
4. How to conduct DH+UV composite aging test
According to the test standards and test experience of component materials, Huayang Testing recommends the test parameters for the composite aging test as follows:
The above-mentioned test can evaluate the quality of parts and materials in a short time, and it is a fast and efficient screening method. Huayang Testing is using the DH+UV composite aging box to conduct ultraviolet high-temperature and high-humidity tests on connector materials for customers, as shown in the figure below (setting parameters: temperature is 85°C, humidity is 85%RH, radiation is 120kWh/ m2, the test time is 1000h).
So far, more and more material manufacturers have begun to pay attention to and carry out the testing of composite test items. It is believed that in the near future, composite aging testing will be included in routine testing items.