How to Design the Management System (BMS)
How to Design the Management System (BMS)
The application range of battery energy storage systems is becoming more and more extensive, but the market conditions they are facing are also becoming more and more stringent. Technical experts from battery management system developer Brill Power analyzed and discussed how to design and build a battery management system (BMS) that ensures longer life, versatility, and availability of battery energy storage systems.
The operation and maintenance of the battery energy storage system requires the use of a battery management system (BMS). The battery management system (BMS) is a combination of electronic technology and software, and is the brain of the battery energy storage system. This article focuses on the battery management system (BMS) used in battery energy storage systems. The most basic function of a battery management system (BMS) is to ensure that the battery remains balanced and safe, and to communicate important information, such as available capacity, to the user or the connected battery energy storage system.
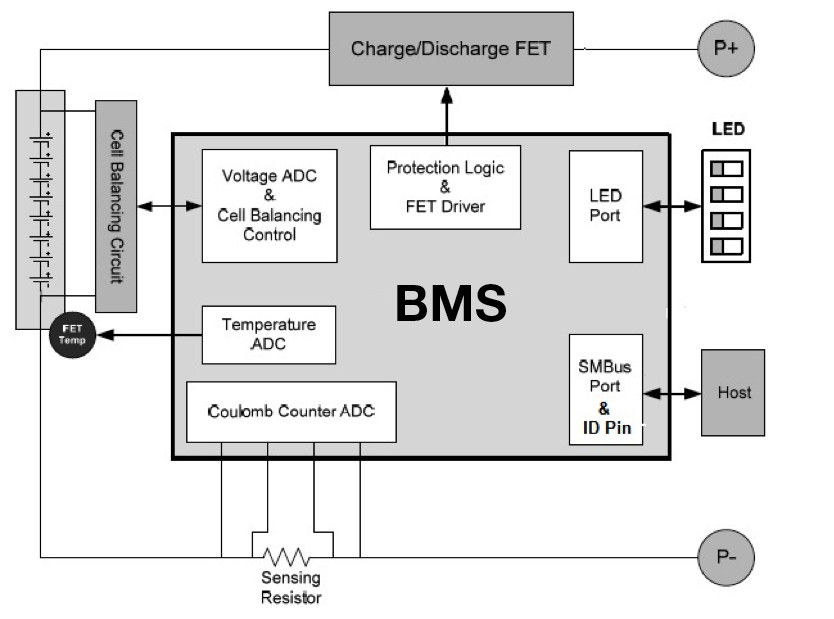
Brill Power is developing and designing battery management system (BMS) hardware
Balancing is necessary because battery storage systems are typically made up of hundreds or even thousands of cells, each with slightly different capacities and resistances. Over time, these differences increase as each battery degrades at a different rate. If the battery voltage is not balanced, it will soon reach the point where the battery cannot be used.
Safety is ensured by keeping the battery within safe operating ranges of voltage, current, and temperature, which is especially important for Li-ion batteries. If a battery is overcharged, or charged at a very low temperature, or charged at an excessively high current or temperature, there is a risk that the battery could malfunction, causing a fire or explosion.
Parameters such as usable capacity and power cannot be measured directly, meaning the battery management system (BMS) must perform calculations based on measurements of voltage, current and temperature. This calculation is known as state estimation, and its results are passed to higher-level systems, such as user interfaces.
Before looking at the considerations for battery management system (BMS) design in more detail, it is necessary to understand the different types of battery management systems (BMS) and the industry requirements that dictate how the design should be done. A balancing approach is often used to classify battery management system (BMS) types, although other design aspects also play important roles, such as different approaches to state estimation and information flow.
battery status
Batteries come in different sizes, which are directly related to their capacity. Lithium-ion batteries, for example, are usually the smallest sized batteries. The lowest voltage of lithium-ion batteries can be as low as 2.5V (such as lithium iron phosphate batteries), and the highest voltage can be as high as 4.3V (such as NMC ternary lithium batteries).
Batteries can be connected in parallel to increase the maximum current of the battery pack. Batteries connected in parallel or in series are often referred to as super batteries.
In general, the voltage of supercells connected in parallel can self-balance and no further management is necessary. Exceptions may include newer batteries like lithium-sulfur batteries, and batteries with flat charge-vs-voltage curves like lithium-iron-phosphate batteries that operate at extreme charge-discharge rates.
Connecting super cells in series will increase the voltage of the battery pack, which is mainly used in high power applications.
Energy storage capacity increases when cells are added to a battery pack configuration. Therefore, adding a battery pack connected in parallel to a superbattery will increase the energy storage capacity of the battery pack, just like putting additional supercells in series.
Battery Management System (BMS) Hardware
balanced approach
After the charging process is complete, passive balancing dissipates energy (as heat) through the resistors, resulting in a consistent battery voltage that would otherwise go into a fully charged battery. The advantage of using this method is the low cost of electronic components. The downside is that the current flow through all the cells is the same, which means that the worst-performing cell in a series-connected battery pack can affect the energy, power, life, and safety of the entire battery pack. Due to the higher current draw of the worst-performing battery, its degradation rate will be accelerated, which may also cause localized hot spots, and lead to reduced capacity of the battery pack and even safety problems. Also, power will be wasted during charging. The passive battery management system (BMS) can only monitor the battery pack current and can interrupt the battery pack current through the disconnect switch in case of failure.
If bidirectional information flow is implemented, system-level parameters such as operating settings may be changed to prioritize battery life or performance. While improving battery life requires fewer charge and discharge operations at the expense of available capacity or power, improving performance requires increasing charge and discharge operations at the expense of reduced battery life.
Active balancing is typically achieved through a low-current bypass, a circuit that delivers lower charge current to a battery that is not yet fully charged, rather than dissipating this energy as heat. The main benefit of this approach is increased charging efficiency, which can be important if the available charging energy must be used efficiently. However, for most application scenarios, active balancing does not justify the added cost of components. As with passive balancing, higher current draw from poorer performing cells accelerates cell degradation and can create hot spots.
Brill Power Receives Patent for Developing a New Method of Battery Control and Management
Brill Power is a spin-off from Oxford University. Their research found that the super battery’s current needs to be constantly adjusted according to the battery’s own conditions. This ensures that all available energy is fully utilized without reducing battery pack life and slows degradation of poorer performing cells.
The safety benefits of full current control include avoiding the formation of hot spots by reducing the current flow on high-resistance batteries, timely disconnecting the battery and any possible failure. This approach also has the benefit of system-level voltage regulation, which enables direct integration of batteries with DC sources such as solar power plants, fuel cells, and other types of batteries, as well as DC loads such as EV chargers. In isolation, the component cost of this approach is higher than that of a passively balanced battery management system (BMS); but at the system level, the cost is lower than that of a passively balanced battery management system (BMS).
The way to reduce the cost of battery energy storage systems is to reduce the size of the battery for a given performance and avoid additional hardware (such as DC/DC converter or inverter). According to Brill Power’s analysis, by extending battery life, the total cost of ownership can be reduced by 60%.
Other approaches to battery management system (BMS) technology include cascaded cell bypass and inverter integration, but due to their limited applicability, they are not discussed further here.
A brief description of the different battery management system (BMS) types
state estimation
Estimation of state of charge (SoC) and state of health (SoH) is based on a combination of battery models and estimation algorithms. The level of complexity and accuracy possible for state estimation and the underlying model of the battery depends heavily on the hardware, which is used here to differentiate the different approaches.
Integrated circuits (ICs) are used for state estimation in most conventional battery management systems (BMS). The integrated circuit is “hardwired” with a specific battery model and state estimation algorithm. The advantage of integrated circuits is low cost, and the disadvantage is that the flexibility and accuracy of system design are limited. And these shortcomings tend to get worse over time. Design flexibility is limited because integrated circuits are typically created for specific batteries with specific specifications.
If the battery type or specification changes, the integrated circuit (IC) also needs to be changed and designed to adapt. The reasons for its limited measurement accuracy and constant degradation are: (1) The state estimation of the integrated circuit is based on a generalized representation of the battery, which does not capture the subtle thermodynamic and kinetic properties of the battery, which may vary depending on the battery manufacturer, specification and batch. (2) The limited computing power of integrated circuits limits the complexity and fidelity of state estimation algorithms and underlying battery models; (3) Battery characteristics change over time, while hardwired Wire IC algorithms fail to capture these properties, resulting in increasingly inaccurate results over time.
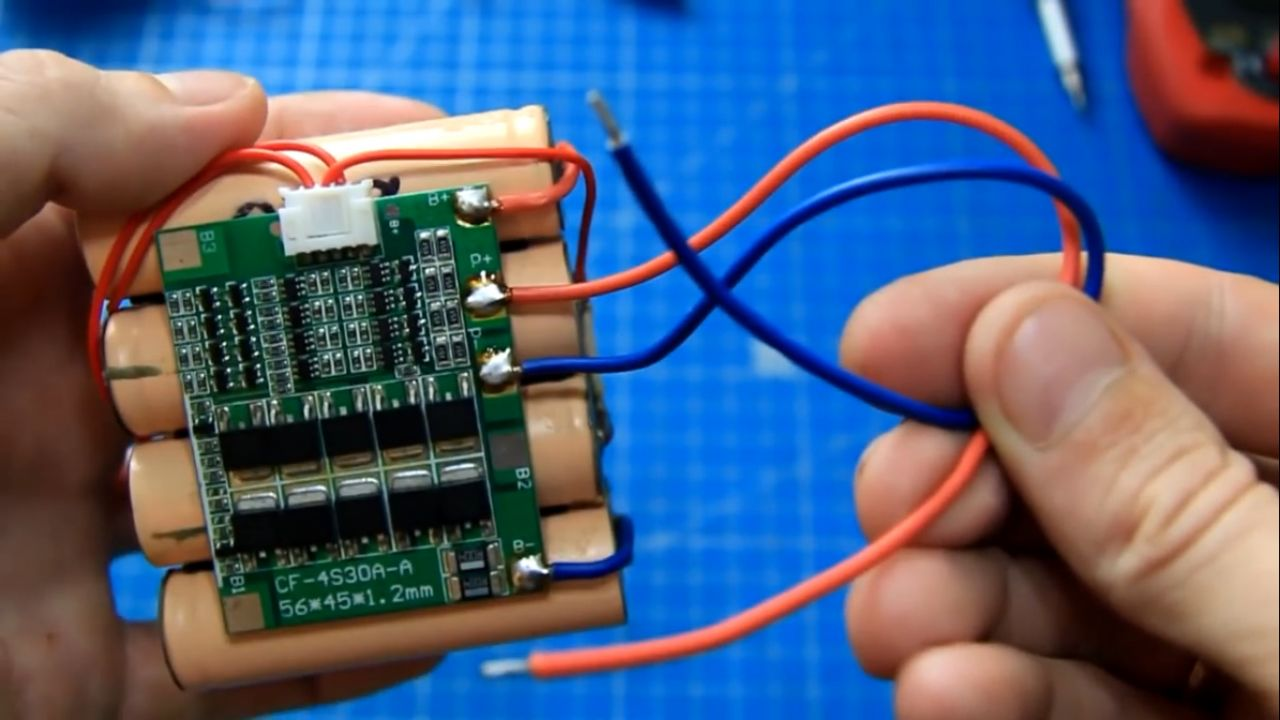
Instead, microprocessors can be programmed with more complex, higher-fidelity battery models and state estimation algorithms that can be fine-tuned to specific battery characteristics and specifications. By updating the parameters of the state estimation algorithm and the battery model, it is possible to adapt to changing battery characteristics, resulting in more accurate power output over time. The hardware can be used with any type of battery for ultimate design flexibility. The downside can be higher component costs, depending on the required functionality and computing power.
Information Flow
One-way information flow is common in most battery energy storage systems: parameter information flows from the battery management system (BMS) to higher-level systems and user interfaces. If the battery manufacturer provides a battery management system (BMS), less low-level information is available, which could be considered sensitive. But the most important information is safety- and performance-related, including metrics like state-of-charge (SoC) and state-of-health (SoH).
If a microcontroller is used, the battery management system (BMS) can process input parameters such as changing operating settings such as maximum and minimum allowable battery voltage or SoC, or even updating the battery model or state estimation algorithm to maintain its accuracy, thus achieving bi-directional Information flow is possible.
Design and development of battery management system (BMS)
Once the appropriate type of battery management system (BMS) has been identified, design and development can begin. The most important factors in battery management system (BMS) design are team and expertise.
Battery management system (BMS) design has traditionally been the domain of electrical engineers, who are indeed the best at designing circuits but often don’t know much about the inner workings of batteries. Designing a perfect battery management system (BMS) requires knowledge and skills in electrochemistry, physics, electrical and electronic engineering, firmware development, and data science.
With the right team in place, the first consideration is compliance with regulations and industry standards, as this affects both hardware and software design. Some regulations and standards are often country-specific.
While most regulations and standards apply to battery storage systems, some regulations apply to all electronic components, including hazardous substance regulations such as RoHS and REACH in Europe. Relevant industry standards mainly depend on the application and system specification. The typical distinction is between residential and industrial energy storage, and whether it is low or high voltage.
Relevant industrial energy storage system standards include IEC62619, UL1973, UL9549 and VDE-AR-E2510-50. Product and functional safety is the most important aspect of these standards. Although the battery management system (BMS) does not need to be certified as a stand-alone component, it does not prevent battery energy storage systems from being certified. It is therefore recommended that future compliance with the standard be tested and assessed by an independent testing and certification body such as DNV.